How 70-year-old Abqaiq Plants transformed to become a 4IR leader
As part of our efforts to become the world’s leading digitalized energy company, Aramco renovated and refurbished our oldest oil processing plant, transforming it into a world leader in the use of Fourth Industrial Revolution technology.
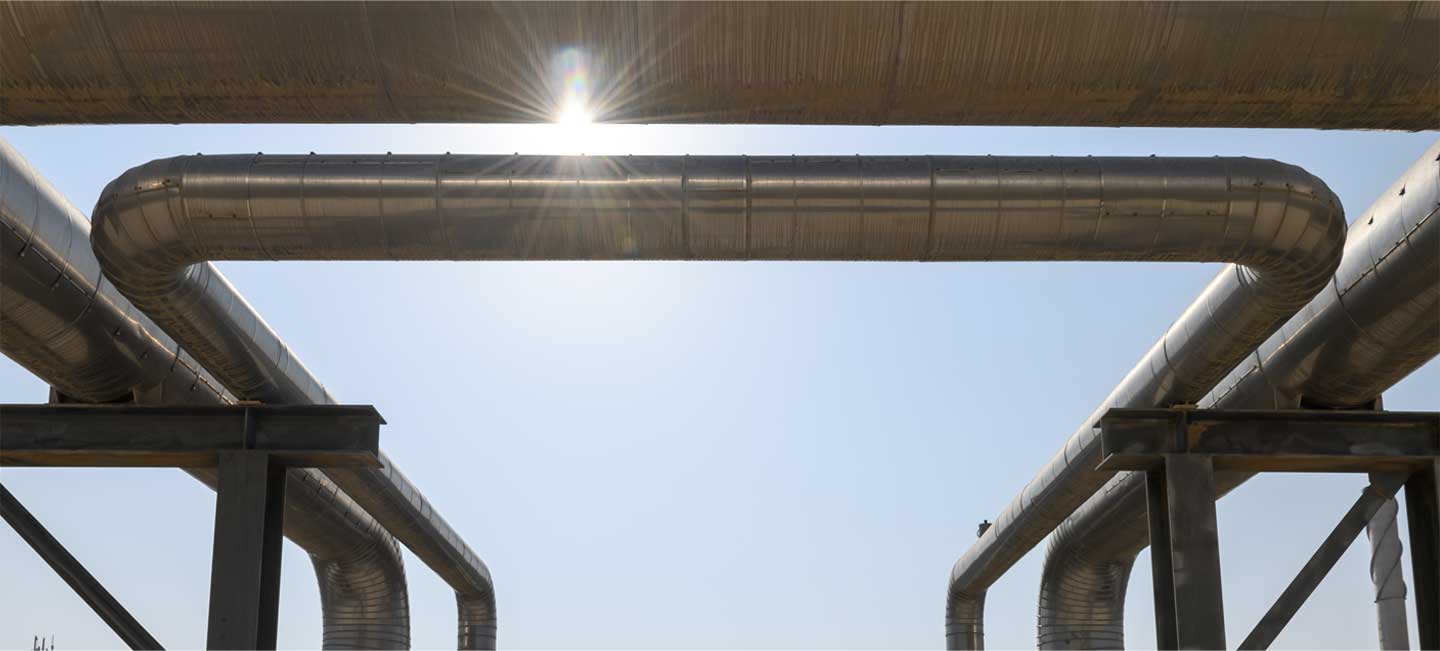
- Abqaiq Plants, the oldest oil processing plant in Saudi Arabia, has harnessed the power of digitalization to enhance its operations; utilizing robotics, artificial intelligence, data analytics, and IIoT
- The use of 4IR technology helped free workers from mundane, sometimes hazardous tasks, allowing them to take on more rewarding roles
- The revamped site gained recognition as a cutting-edge technology leader and is our latest facility to become part of the World Economic Forum’s Global Lighthouse Network
Abqaiq Plants is the largest crude stabilization plant in the world, and a cornerstone of our operations.
It provides around 5% of global oil supplies and stabilizes half of Saudi Arabia’s daily oil production. However, at 70 years old, it is also our oldest oil processing facility. This naturally presented a few challenges on its journey toward becoming more digitalized — a process essential to maintaining peak performance.
Given the facility’s importance, it has played a central role in our digital transformation program, which harnesses Fourth Industrial Revolution (4IR) technologies to increase efficiency, and is integral to our goal to become the world’s leading digitalized energy company. The result, even in the face of the unique challenges the project presented, has been global recognition, with the World Economic Forum (WEF) acknowledging it as a global leader in 4IR in 2021.
Inspiring tomorrow’s technology leaders
The World Economic Forum (WEF) highlights world leaders in 4IR technology through its Global Lighthouse Network (GLN). They've reported that many companies have struggled with taking their 4IR plans beyond the pilot stage. By showcasing successful projects, and supporting the sharing of expertise, the aim of the GLN is to inspire companies and industries to embrace 4IR technologies and their potential to transform their operations.
Abqaiq Plants is our third site to be admitted to the GLN by the WEF's panel of global experts, following the Khurais oil field and the 'Uthmaniyah gas processing plant. All three sites are examples of how 4IR technology can be used to render oil and gas production more sustainable.
“Abqaiq Plants' achievement of becoming a Global Lighthouse is a testament to Aramco's efforts to boost digitalization and promote the use of Fourth Industrial Revolution technology, with the aim to reinvent our industry and shape the next generation of smarter and more efficient oil and gas production,” says Nasir Al-Naimi, President Upstream.
Unique challenges
A successful digital transformation starts at the infrastructure level. The technology infrastructure of most old oil and gas facilities relies on legacy and de-centralized systems to carry out its processes.
What these old and outdated systems do is distribute critical data across several systems and applications inside the facility — meaning it is hard to easily access data, and interpret it or use it in collaborations.
Working with this infrastructure, employees at Abqaiq Plants had to manually analyze the data in order to troubleshoot or optimize processes. They were also used to legacy systems, and processes developed over many years, and to carrying out sometimes mundane, occasionally hazardous, tasks.
Transformation roadmap
Reinventing Abqaiq Plants meant creating the right roadmap to help ensure a smooth digital transformation journey.
This roadmap incorporated many approaches, including: using a centralized technology management database to identify promising technologies, collaborating with technology providers on pilot projects, and establishing a dedicated 4IR technology center to accelerate collaboration and knowledge sharing.
The roadmap also helped encourage the sharing of data across teams to enhance the value of the technologies used, and supported the development of new and innovative solutions. The availability of data across teams was improved through the use of an Industrial Internet of Things (IIoT) infrastructure. And helping employees embrace the use of technology was always front and center, with new skill development encouraged through dedicated courses and programs.
Old facility, new tricks
Global technology-focused recognition was not on the agenda when Abqaiq Plants was built in the 1940s. Indeed, few had considered that we might one day connect-up industrial machines using radio signals so they could ‘talk’ to computers. But that is just one aspect of what 4IR technology allows: using industrial Wi-Fi, machines share crucial performance data, and then relay that to artificial intelligence (AI) systems that make adjustments in order to increase efficiency or which can predict faults preemptively.
Wireless communications have evolved with time, progressing from point to point communication to mesh technology — a network that enables several devices to connect and transfer data simultaneously. The benefits of that include better performance, greater flexibility, and wider coverage for industrial applications. Abqaiq Plants’ systems have also evolved from de-centralized systems to the latest state-of-the-art distributed control systems, which offer greater interface and connectivity capabilities. Higher efficiency, lower costs, and enhanced safety are among the numerous operational benefits that advanced connectivity brings.
Enhancing performance with AI
By harnessing the transformative power of big data and analytics, Abqaiq's manufacturing processes have been transformed, enabling it to innovate and improve. That includes using AI to monitor equipment performance, so manual inspections are not carried out unnecessarily. Using AI in this way has also eliminated production impacts caused by equipment failure.
The site also uses a machine learning model trained on 1.7 billion data points to carry out simultaneous optimization of 18 crude stabilization units. Previously managed manually, these units now run more efficiently because the AI can analyze the data and perform an adjustment faster than any human.
More digitalized, more human
4IR technology offers a great opportunity to free workers from mundane tasks, equipping them with new skills and allowing them to take on more rewarding roles and responsibilities. At Abqaiq Plants, a safety inspector can retrain as a drone pilot, flying an unmanned vehicle to the top of a facility to carry-out inspections, rather than climbing scaffolding to reach it. They can then use their experience to examine the data and identify potential faults. Robots and drones are now the norm and are used to perform almost a third of routine operations checklists, such as safety inspections.
Employees also use AI to monitor the oil stabilization process — a partial distillation process that makes crude oil suitable for storage or pipeline transportation.
Intelligent Sensors monitor every part of the stabilization process and AI analyzes the data to detect abnormalities, identify the cause, and provide recommendations on corrective actions. The system might decide, for instance, that less steam is required to stabilize a particular oil stream. Reducing the steam used means less energy is needed and the environmental footprint is lower.
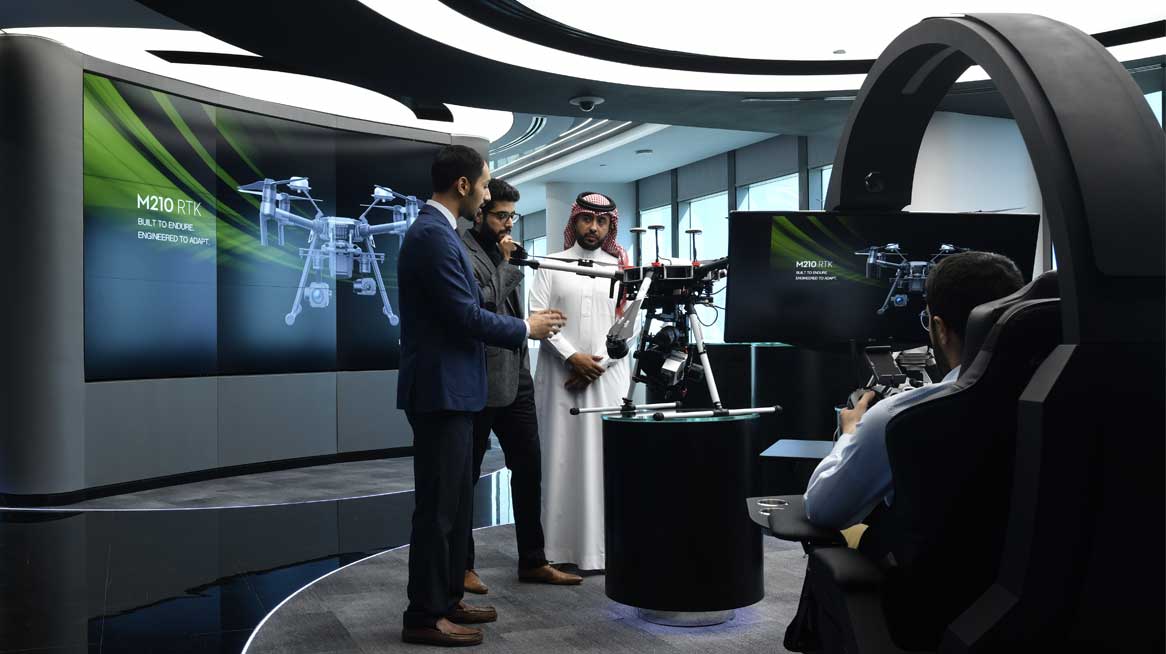
Drone training
“Aramco recognizes the importance and power of strategically deploying 4IR, to improve efficiency and sustain demand in a safer and more reliable way and enable us to reduce our GHG emissions,” says Khaled Al-Buraik, Senior Vice President Southern Area Oil Operations.
“This recognition by the World Economic Forum extends to the talented teams from Abqaiq Plants who transformed ideas and concepts into reality, as well as Aramco’s wider corporate organization which supported and enabled these efforts.”
Driving energy efficiency and emissions reduction
The world’s demand for energy is increasing, and so is the need for more-sustainable ways to produce that energy. Fortunately, big data, advanced analytics, and automation can be leveraged to help maximize efficiency.
Automated systems can make subtle changes to production in an instant — far more quickly than a person, who would have to analyze the data, interpret its meaning, make a decision, and then put it into action. Abqaiq Plants used advanced data analytics to predict real-time crude oil quality and make small, fast adjustments to production, and implemented various other initiatives to boost efficiency. This helped achieve a 31.8% reduction in carbon intensity between 2019 and 2022.
Abqaiq Plants demonstrates the power of 4IR
Abqaiq Plants’ success demonstrates just how important 4IR technology is to the overall efficiency, productivity, and future-proofing of energy facilities.
The founders of Abqaiq Plants would scarcely have been able to imagine the technology that it uses today. But, if a facility well into its seventh decade can be turned into a global beacon for 4IR, then any industrial facility, anywhere in the world, could potentially do the same.
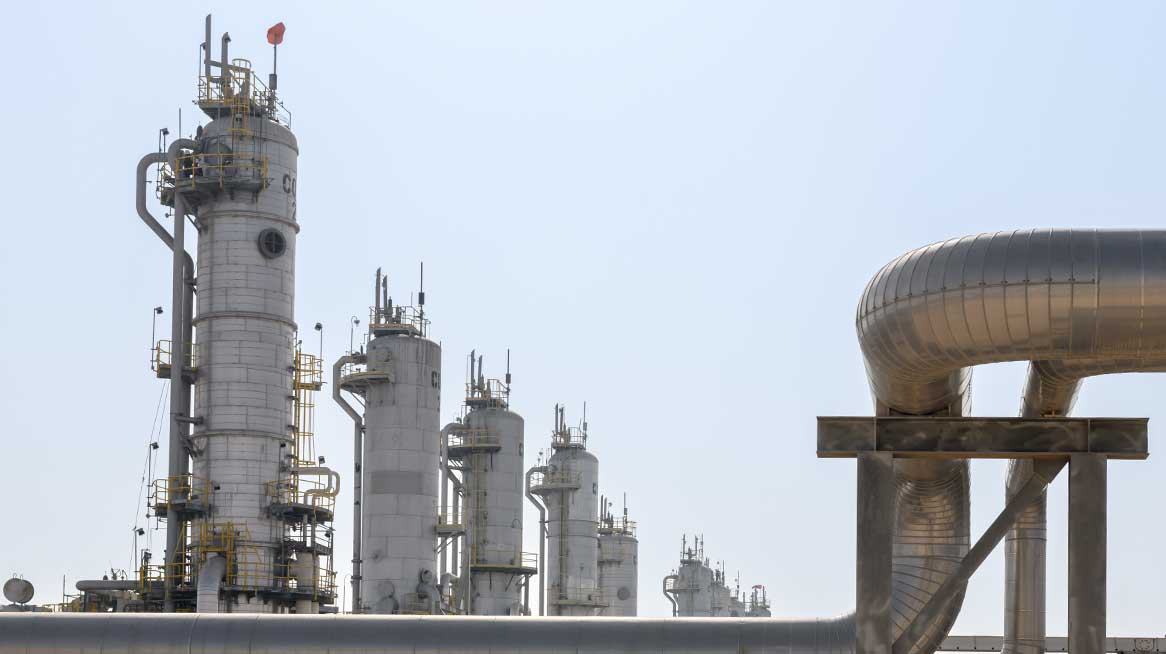
Abaiq facility